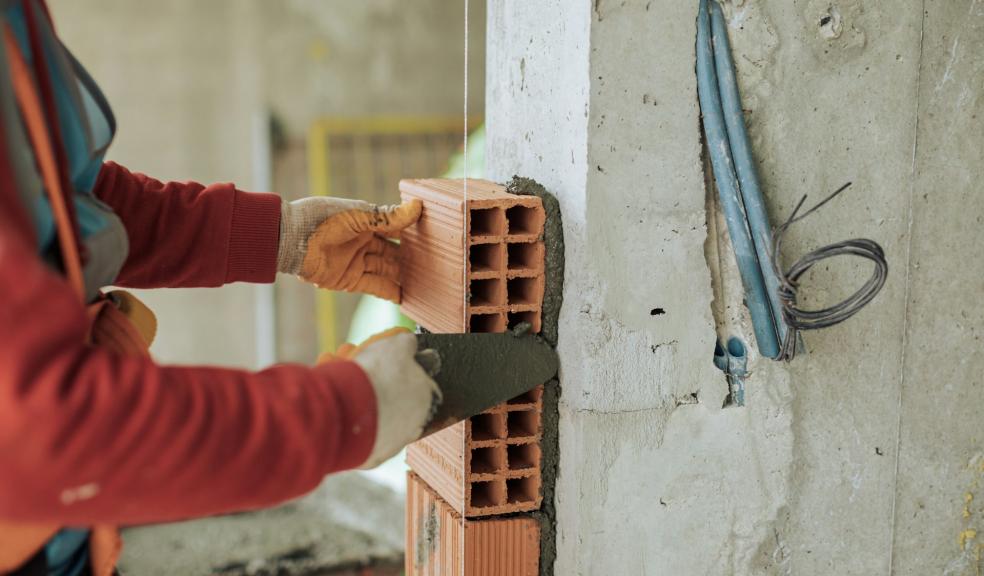
Hidden Problems That Can Derail Your Extension Plans
Home extensions often seem straightforward at first glance. Plans are drawn up, materials are costed, and timelines are agreed upon. Then, the work begins, and so do the surprises.
Unexpected problems can stall progress or inflate budgets. Some are minor, but others carry serious safety, legal or financial consequences. Many issues lie hidden until demolition or excavation work starts. Others are missed entirely until a contractor flags them on-site.
Planning helps, but awareness of less visible risks makes a real difference.
Structural Surprises in Older Homes
Older properties come with character but hide faults that don't always appear on surface inspections. Joists may look fine from below, but have rot or infestation inside the walls. Load-bearing walls are sometimes wrongly assumed to be non-structural. Minor cracks can signal deeper movement, and historical repairs may not meet current standards.
Before signing off on plans, it is worth getting a building survey that focuses specifically on structural elements. Standard surveys are often not detailed enough. A structural engineer can clarify what can stay and what needs reinforcement or removal.
Timber floors, cavity walls, and older roof structures are worth checking. This prevents the shock of mid-build strengthening work that halts progress and adds unplanned cost.
Planning Delays and Compliance Checks
Planning consent is often just the beginning. Once your project moves to construction, building regulations come into play. These are separate from planning and cover how work is carried out.
Extensions often require inspection at several stages, such as foundations, insulation, drainage and final sign-off. If work fails inspection, it cannot proceed until the issue is fixed. This delays trades, disrupts schedules and puts pressure on budgets.
Additional rules apply for homes near boundaries or in conservation zones. Party Wall Agreements, heritage restrictions, or tree protection orders can surface mid-project. These all demand time, communication, and sometimes reworked plans.
Getting professional help early on with regulatory requirements avoids setbacks later. Many delays stem from misunderstandings around what permissions or inspections are required and when.
Dangerous Legacy Materials Hidden in Roofs and Walls
Older materials can pose safety risks and legal issues if they remain unnoticed. Extensions that involve opening up ceilings, removing external walls, or modifying rooflines will likely expose what has been left behind from decades past.
Asbestos roofing is one of the most common finds in garages, porches, and outbuildings. While it may seem stable to the eye, it becomes dangerous when disturbed. Cutting, drilling, or removing asbestos materials without proper control risks health and safety.
Proper asbestos roof removal requires licensed professionals and strict regulations. Homeowners or contractors without experience in this area can unknowingly break the law.
In many cases, continuing with an extension relies on replacing asbestos roofs safely. This ensures legal compliance, protects all trades involved, and prevents delays tied to health investigations or work stoppages.
Other materials worth flagging include lead-based paint, uninsulated wiring from earlier periods, and fibreboard insulation that lacks flame resistance. Each of these needs different approaches, from testing and disposal to modern replacement.
Budget Risks from Late Discoveries
Delays are not the only issue once problems surface. Costs can climb quickly when new work becomes necessary. For instance, a builder quoting for a straightforward single-storey extension will not be pricing for structural redesigns or the controlled removal of asbestos roofing. If scaffolding needs to stay up longer or extra skips are required, costs grow again.
Unexpected material upgrades and additional labour days shift a project's financial shape. Specialist tasks like asbestos roof replacements require trained teams, licensed equipment, and proper waste management. These are all outside the normal building scope and must be budgeted realistically.
Building a buffer for specialist fees, planning revisions, or re-inspections will ease pressure if things do not go exactly as planned.
Site Limitations That Cause Scheduling Chaos
Even with plans approved and materials ordered, physical limitations on site can cause problems. Tight access to rear gardens may prevent diggers from getting through or prevent larger roof sections from being lifted into place. Neighbours might object to scaffolding overhanging their land, delaying works while agreements are sorted.
In rural areas, deliveries are affected by road restrictions or vehicle limits. It may be hard in towns to store bulk materials without causing obstruction or breaching site rules. These challenges usually come down to logistics, but they slow everything down.
Planning with your contractor helps reduce the chance of disruption. That means checking access measurements, understanding what machinery needs to reach the site, and speaking to neighbours where required.
Keep Your Extension on Track with Informed Preparation
Extension projects carry risks that do not always appear on paperwork. Some cannot be prevented entirely, but better preparation makes many delays and complications manageable.
Getting full structural surveys done before committing to work avoids surprise repairs. Engaging early with planning consultants helps avoid compliance problems. Checking for hazardous materials like asbestos roofing before building begins can keep everything legal and safe from day one.
Do not assume everything behind the plasterboard or under the tiles will meet current standards. Older properties need a closer look. Speak with experienced trades and use qualified inspectors wherever necessary. What you do before work starts often determines how smoothly it finishes.